In the modern manufacturing landscape, green sand casting has emerged as one of the most reliable and cost-effective methods for producing complex metal components. At the forefront of this technology is IDP Company, a leading industrial foundry known for combining innovation, quality, and environmental consciousness. This article explores how IDP leverages green sand casting technology to meet the demands of various industries while maintaining sustainable production practices.
What is Green Sand Casting?
Green sand casting is a metal casting process that uses moist sand (clay and water) as the mold material. Despite the term “green,” the sand is not color-related—it’s called “green” because it is not dried or cured before pouring molten metal into the mold. This method is popular due to its reusability, low cost, and flexibility in producing complex shapes.
IDP’s Green Sand Casting Process
At IDP, green sand casting is more than just a traditional technique. The company integrates modern technologies and rigorous quality control to ensure consistent and high-performance results.
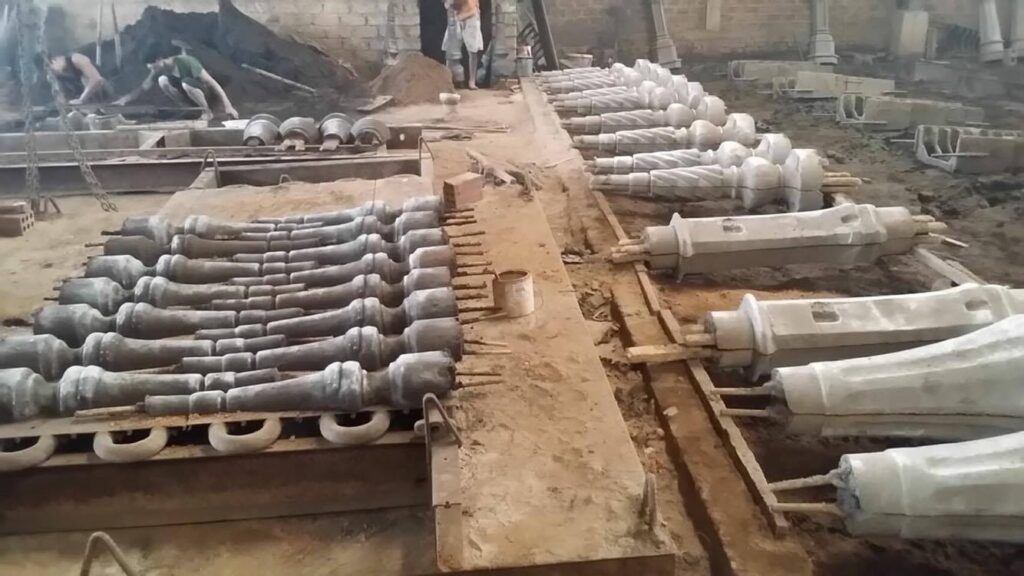
Lamppost made by green sand casting technology
1. Advanced Mold Preparation
IDP uses high-speed molding lines and automated sand mixing systems to ensure the sand maintains optimal moisture and bonding properties. The result is molds with exceptional dimensional accuracy and surface finish.
2. High-Quality Raw Materials
Only premium-quality sand, bentonite clay, and additives are used. This guarantees better compaction, minimal defects, and extended mold life.
3. Precision Pouring and Cooling
With computer-controlled pouring systems, IDP maintains consistent metal flow rates and accurate temperatures, reducing porosity and enhancing mechanical properties.
4. Post-Casting Finishing
Once the casting cools, the sand is separated and reused, while the metal part undergoes cleaning, heat treatment, and machining to meet customer specifications.
Benefits of Green Sand Casting
- Cost-Effective Production: Reusable materials and automated processes help reduce waste and manufacturing costs.
- Versatility: Suitable for a wide range of metals including cast iron, steel, aluminum, and more.
- Environmental Sustainability: Over 90% of the sand is recycled, minimizing environmental impact.
- Custom Solutions: IDP provides tailored casting solutions for automotive, machinery, agriculture, and other sectors.
Why Choose IDP?
With decades of experience, IDP stands out as a trusted partner in the metal casting industry. The company is committed to continuous improvement, customer satisfaction, and sustainable manufacturing practices. Our green sand casting technology enables fast lead times, consistent quality, and scalable production—from small batches to large-volume runs.
Conclusion
IDP’s investment in green sand casting technology reflects its dedication to quality, innovation, and the environment. Whether you’re seeking high-performance parts or a reliable manufacturing partner, IDP delivers world-class solutions through one of the most efficient casting processes in the industry.