The Production Process of Cast Iron LampPost at IDP Casting Company
At IDP Casting Company, we specialize in the production of high-quality cast iron lamp post, combining advanced foundry technology with artistic craftsmanship. Our products are widely used in public spaces, parks, urban infrastructure, and heritage restoration projects. Below is a detailed overview of our production process:
1. Design and Customization cast iron lamppost
At IDP, each lamp post begins with a precise design process. Our engineering and design team works closely with clients to develop 2D drawings and 3D models, based on standard designs or customized specifications. We ensure that every detail — from structural requirements to ornamental elements — is carefully considered.
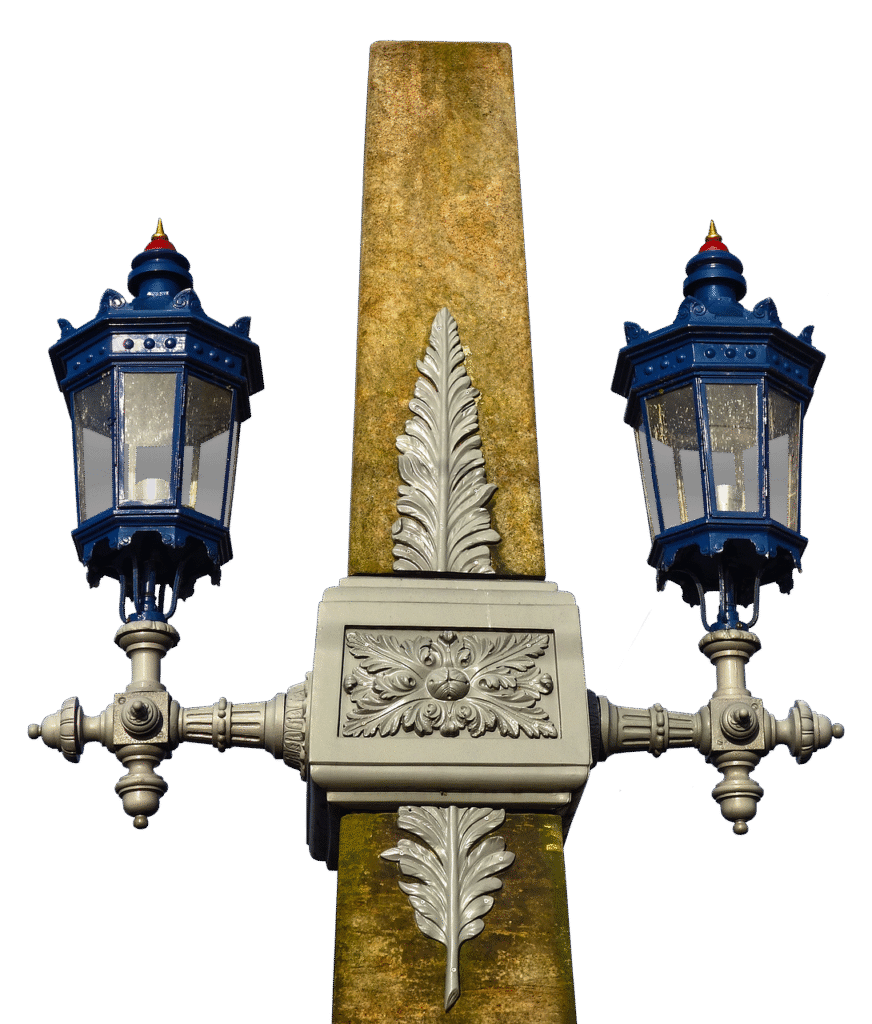
3D design of lamp
With some special projects , we get the cast iron lamppost and make the file by 3D printing technology . After that , base the customer’s requirements , our designers will restore and adjust the 2D file . The 3D file could be make and 3D draft of the product will be printed by plastics .
2. Cast iron lamppost – Pattern Development
Once the design is approved, we create the pattern — a replica of the lamp post — using wood, resin, or aluminum. These patterns are crafted with high accuracy to ensure the final casting meets dimensional and aesthetic expectations.
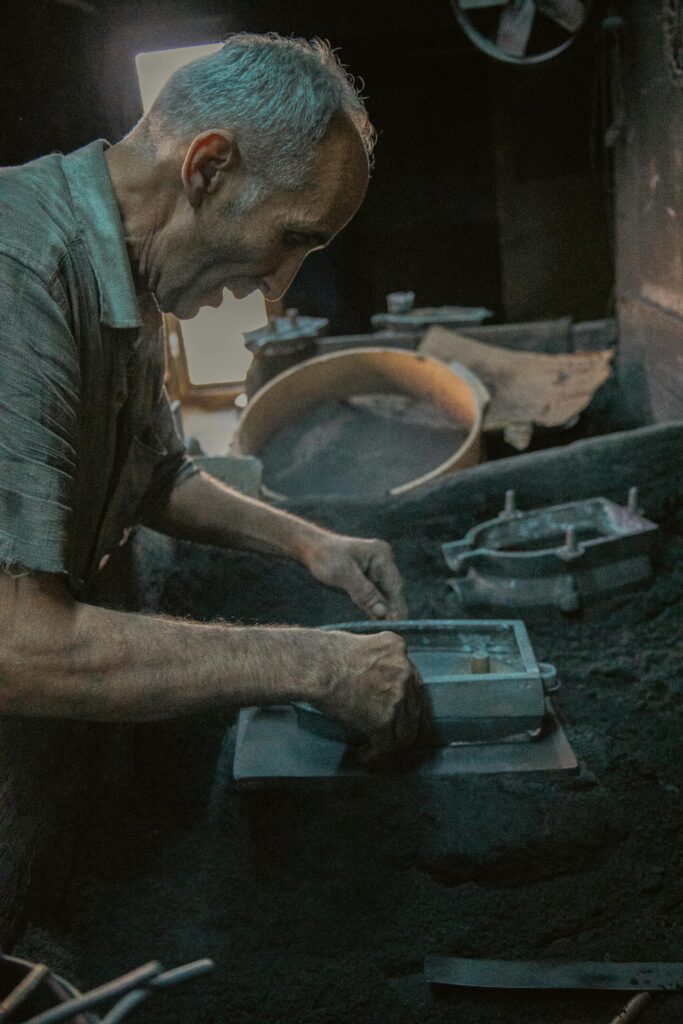
Making the sand molding from cast iron mold
Depending on the quantity and continuity of the project, we will advise customers on different mold materials. And of course, the price and durability are also different.
3. Sand Molding
We use green sand or furan resin sand molding techniques, depending on the complexity and size of the lamp post. The mold, formed by packing sand around the pattern, creates a cavity into which the molten iron will be poured.
With lamppost made by LFC technology , the progressing needs more than some steps , like : make the foam parts , assemble them and vacuum ….
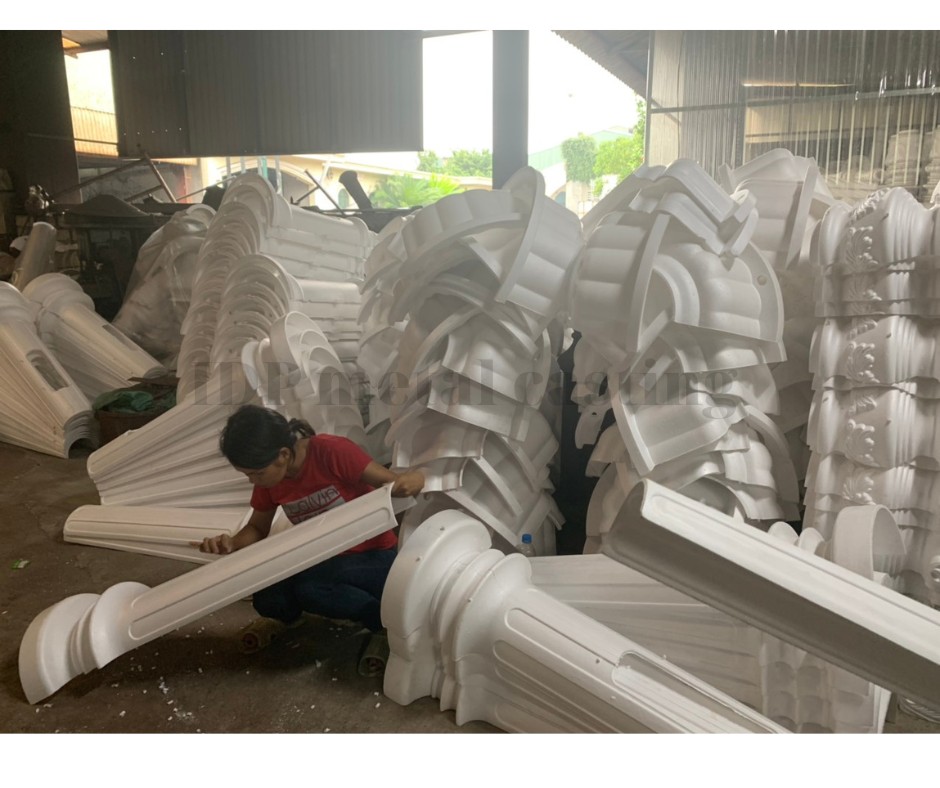
Foam part of lamppost
4. Iron Melting and Pouring
Our foundry uses induction furnaces and clay oven to melt high-grade pig iron and scrap metal. The molten iron is alloyed with specific additives to improve strength and corrosion resistance. Once the iron reaches the optimal temperature, it is poured into the molds under strict safety and quality controls.
5. Cooling and Mold Breakout
The casting is allowed to cool naturally within the mold. Cooling times are controlled to reduce internal stress and ensure casting stability. After cooling, the sand mold is broken, and the raw casting is extracted for further processing.
6. Cleaning and Fettling
The cast lamp posts go through shot blasting to remove sand residues, surface scale, and any impurities. Risers and gates are removed, and surface imperfections are manually corrected to ensure a smooth and uniform finish.
7. Machining and Surface Treatment
Where required, machining operations are carried out on flanges, mounting holes, or threaded sections. We then apply corrosion-resistant coatings such as zinc primer and outdoor-grade powder coating or industrial paint, ensuring long-lasting durability in various weather conditions.
8. Assembly and Final Inspection
Multi-part lamp posts are assembled and inspected for alignment, strength, and finish. Our quality control team conducts dimensional checks, surface inspections, and mechanical tests to meet both national and international standards.
9. Packaging and Delivery
Finished lamp posts are packed using wooden crates or steel frames to prevent damage during transportation. We ensure timely delivery to project sites, both domestically and internationally.