Resin sand casting is a modern metal casting technique that has revolutionized the foundry industry by improving mold quality and production efficiency. Unlike traditional green sand casting, this method uses a mixture of resin and sand to create stronger, more precise molds.
What Is Resin Sand Casting?
Resin sand casting, also known as no-bake casting, involves mixing resin binders with high-quality silica sand. The mixture is then packed around a pattern and allowed to cure, forming a rigid mold. This process allows for the casting of complex shapes with smooth surfaces and tight dimensional tolerances.
Advantages of Resin Sand Casting
- High dimensional accuracy: Resin sand molds maintain shape and size better, reducing the need for post-processing.
- Superior surface finish: The resin-bound sand provides smoother surfaces compared to green sand.
- Flexibility in design: Ideal for complex geometries and large castings.
- Less moisture-related defects: The no-bake process minimizes defects such as porosity and gas holes.
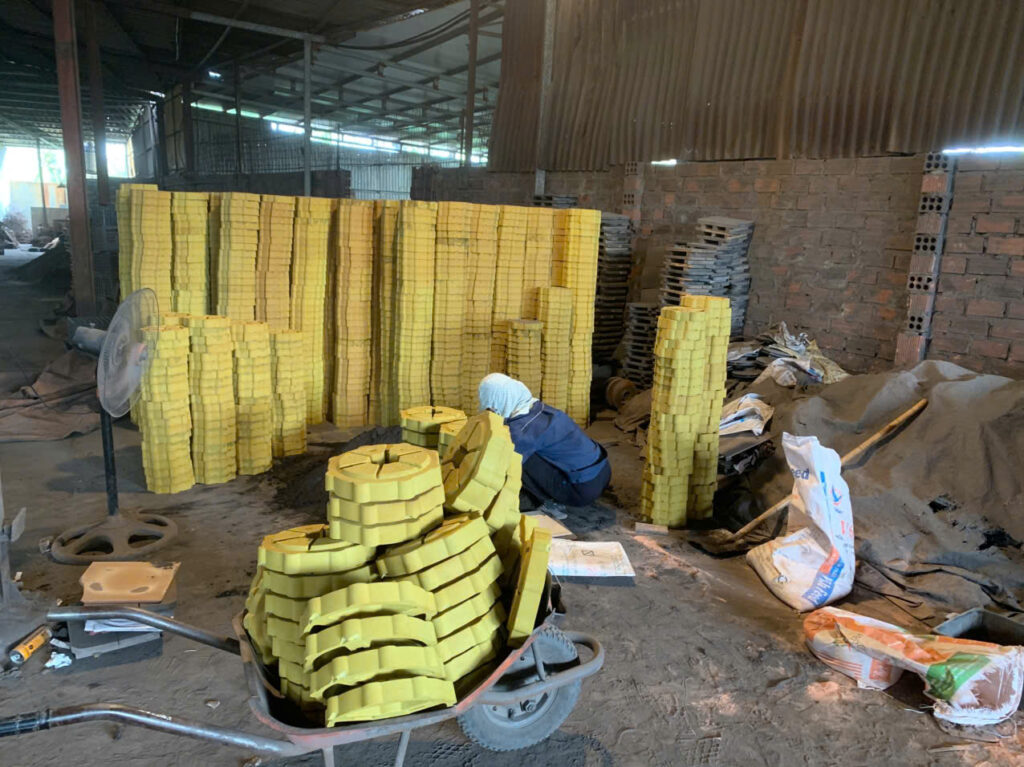
Resin Sand Casting Process Steps
- Pattern making – A model of the final product is created.
- Sand mixing – Resin is added to dry sand and mixed thoroughly.
- Mold forming – The sand-resin mix is packed around the pattern and cured.
- Mold assembly – The mold halves are joined and prepared for pouring.
- Metal pouring – Molten metal is poured into the mold cavity.
- Cooling and cleaning – After cooling, the casting is removed and cleaned.
- Finishing – Any excess material is removed, and the final product is machined if necessary.
Applications of Resin Sand Casting
This method is widely used in the automotive, aerospace, machinery, and energy sectors. It is particularly suitable for producing engine blocks, pump housings, and large industrial components.
Conclusion
Resin sand casting combines traditional foundry techniques with advanced materials to deliver high-quality metal parts. Its advantages in precision, efficiency, and versatility make it a preferred choice for manufacturers seeking reliable and scalable casting solutions.